If you visit a factory or logistics center, you will observe how a product or parcel box moves from one place to another. How is it possible to handle thousands or millions of products daily? More time and labor would be necessary if it were a manual process. Also, it cannot offer you a high outcome. Thus, there’s a need for a conveyor belting system. Among different types, rubber conveyor belts are the most common.
There are various types of conveyor belt material. Plastic, steel, and rubber are the most common types. However, rubber has multiple advantages over other materials. Because of this, rubber conveyor belts are a better option in various applications. People widely use it in stores, industries, and mines. Synthetic rubber blended with other chemicals can produce a robust, flexible, and durable rubber compound. Mixing fabric layers allows you to create high-strength conveyor belts. These belts are excellent for moving heavy load items.
This article mainly focuses on the production processes of rubber conveyor belts. Before jumping into the main processes, it will first go through how a conveyor system works. Then, step-by-step, you will learn more about the real-world production process of rubber conveyor belts.
Understanding the Conveyor System
A conveyor system automatically transports an object from one place to another. You would be surprised to know that this system is used in every factory in the world today. To keep up with the times and to survive in business, you must ensure production speed and product quality. A conveyor system plays a huge role in this task. It consists of 4 parts.
(1) A conveyor belt on which it carries objection from one location to another.
(2) Rollers typically support the conveyor belt. It guides the belt as the object moves.
(3) A pulley uses the tension and direction to drive the conveyor belt.
(4) A motor powers this whole system.
In a typical scenario, the system automatically runs when you start the motor. However, you can control it according to your requirements.
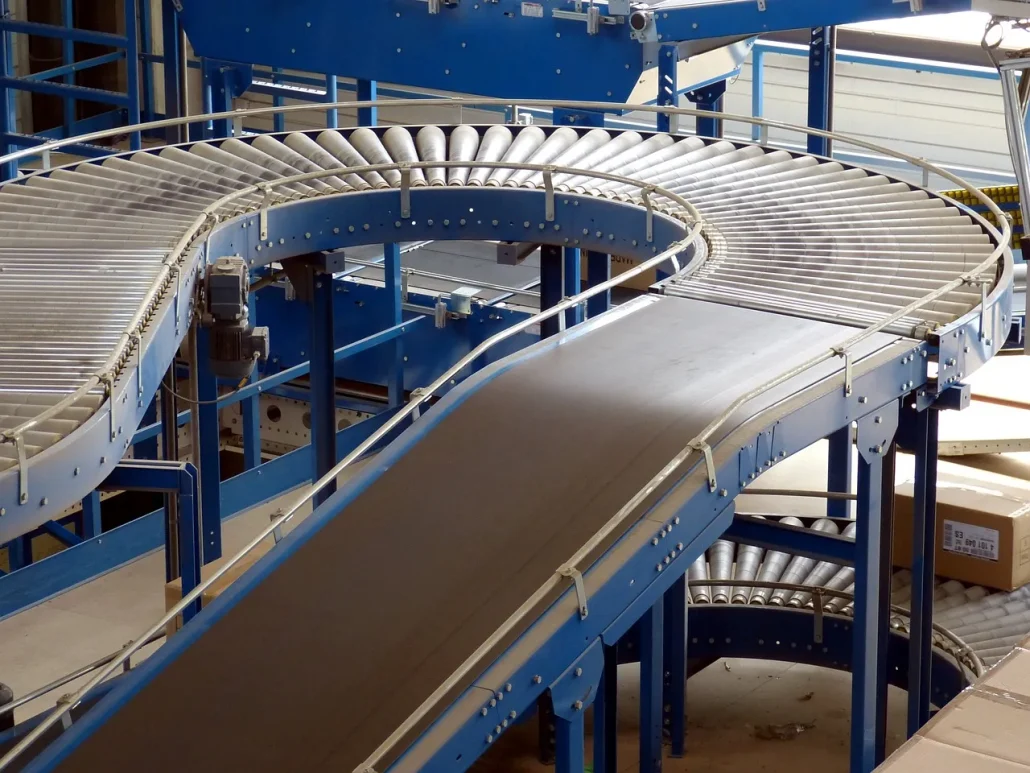
Rubber Conveyor Belts Manufacturing Process
Rubber conveyor belts are typically made from layers of rubber and fabric. The rubber provides durability, while the fabric gives the belt shape and strength. The manufacturing process generally has five significant steps.
Step #1 Mixing
The process starts by mixing various raw materials in a chamber, which is also known as a Banbury mixer. This chamber is connected to a motor that rotates very quickly. Multiple heating mechanisms surround it. Speed and heating typically produce a uniform, nice, plain rubber compound.
This step is critical for two reasons. First, the correct mixture allows you to shape the material quickly. Accurate mixing of plasticizers plays a crucial role here. Second, the mixture determines the properties of the final rubber conveyor belt.
This mixture has different types, depending mainly on your needs and budget. For example, sulfur helps in vulcanization in this mixture, making your belt more flexible and strong. Carbon black, on the other hand, increases the strength and wear resistance of the belt.
You can also use different types of plasticizers if you want. This makes rubber conveyor belts more flexible, and you can easily shape the mixture. In addition, various types of antioxidants and anti-aging agents can also be used. These usually protect your rubber belt from heat and sunlight.
After mixing, the molten rubber compound is cooled. Then, it is stored in sheets. The sheets are removed as required and prepared for the next steps.
Step #2 Calendaring
Calendering is a popular shaping method. Rubber conveyor belts are also made into sheets using this method. This method ensures that your rubber conveyor belt gets the correct thickness and strength.
The calendaring process typically involves passing the rubber through heavy rollers. These rollers press and stretch the material to create smooth, uniform sheets. This method is widely popular in the rubber, textile, and plastic industries. It is an excellent method for making conveyor belts, tire linings, coated fabrics, and waterproof materials.
You prepared the rubber compound in step 1. Now, you can feed it into the calendaring machine. It will pass through several rollers that press it into thin layers. During this stage, you can also add fabric layers. These fabric layers are generally made of polyester, nylon, or cotton. You can choose the materials based on your project needs. Note that adding a fabric layer strengthens your belt and prevents it from stretching.
Several factors must be considered when calendaring. Roller temperature, pressure, speed, and fabric alignment are crucial. The correct temperature, pressure, and speed ensure the consistency of the material. Therefore, Rentone Belt always ensures professional manufacturing. Because of this, our customers receive the highest-quality product.
Step #3 Laminating
Now, you have your rubber sheet compounds ready from the previous step. It is time for laminating. What is laminating? Laminating is a process of adding different layers of materials. You must ensure your belt is strong enough to work in the conveyor system. Therefore, two or more layers of rubber and fabrics are added to strengthen the belt.
In this step, you will need a laminating machine to stack the layers. During the process, rubber and fabric layers are stacked together. A bonding agent ensures the layers adhere strongly to one another.
This bonding agent is typically an adhesive. Special bonding agents or adhesives are used for rubber conveyor belt manufacturing. Rentone Belt always ensures top-quality adhesives, so its product lasts longer.
Properly aligning the layers is also crucial when laminating them. Otherwise, your rubber conveyor belt may have various weak spots. The laminating machine applies high pressure to bond the layers firmly during the process.
Step #4 Vulcanizing
Vulcanizing is the most crucial step in manufacturing rubber conveyor belts. It makes the rubber more robust and resistant to heat and chemicals.
Once the laminated belt is ready, you can put it in a laser press. High heat and pressure are applied. This way, you can change the rubber’s molecular structure and make your belt more flexible.
If you do not do this step, your rubber belt will not have sufficient strength to do its job. It might be weak or wear out quickly. However, vulcanization ensures that your belt can handle harsh working conditions.
Step #5 Checking and Packing
Once the rubber conveyor belts are vulcanized, they undergo a quality check. Professional inspectors at Rentone Belt ensure that the products are 100% tested. They check for defects, such as air bubbles, cracks, or uneven thickness, and test the belt’s strength and flexibility.
If the belt meets all standards, it is cut into rolls of different lengths, depending on your demands. Then, these cut rubber conveyor belts are packed and prepared for shipping.
Note that a high-quality rubber conveyor belt must pass the strict test. It comes with the necessary test documents for the products. Always ensure that you have checked these documents before purchasing.
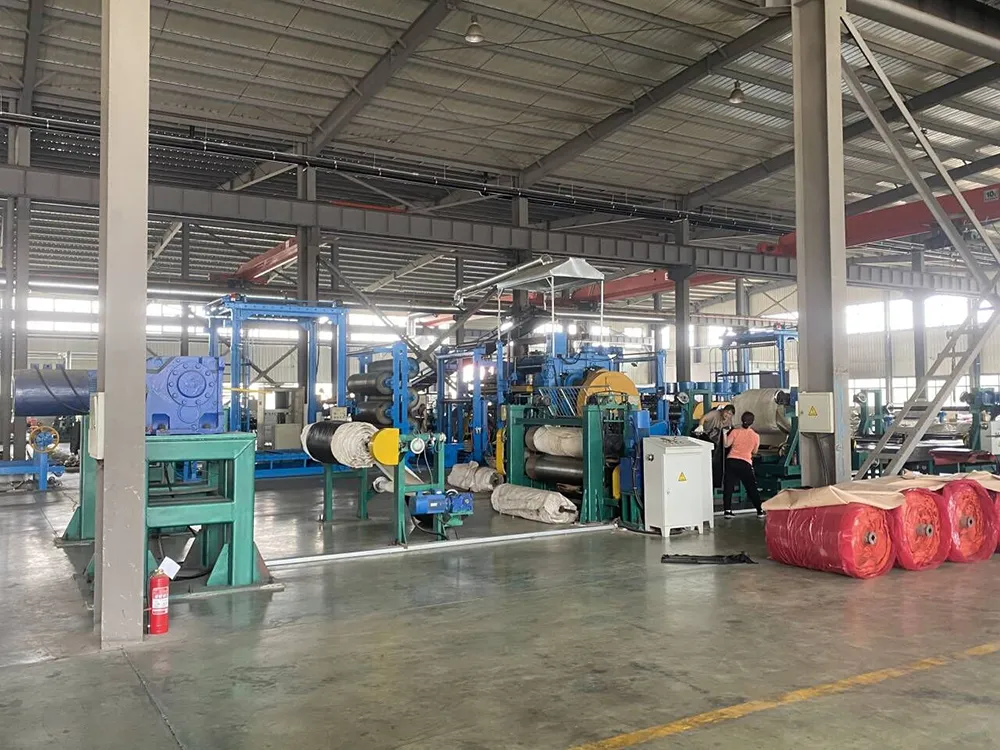
Why Choose Rentone Belt?
Rentone Belt is a leading manufacturer of various types of conveyor belts. Their main products are fabric, steel cord, solid woven, and unique conveyor belts. Rubber conveyor belts are a type of fabric conveyor belt.
There are various reasons why you should choose Rentone Belt. First, this company only focuses on making conveyor belts. As a result, they give you a wide range of options to choose from. Second, they specialize in the highest quality of production. The quality control and testing facilities are advanced and well-maintained by professionals.
Rentone Belt offers you a very competitive price range. You can get the best pricing for high-quality conveyor belting compared to other brands. Finally, their customer support is well-trained and ready to serve you 24 hours. You can reach them through all popular mobile software and emails.
Summary
Rubber conveyor belts are widely popular in many fields. From workshops and mines to construction sites, people use them a lot. As you know, the primary purpose of this tool is to speed up the process. Because of this, you can ensure productivity and efficiency.
Rubber is strong, flexible, and very resistant to heat and chemicals. Because of this, there is a massive demand for it compared to metal or plastic. Rubber conveyor belts usually come in rolls. You can cut them later based on your installation requirements.
This article briefly discusses the production process of rubber conveyor belts. As you know, it comes through five major stages. First, you will mix the raw materials and make a rubber compound. Then, you can use a calendaring machine to give it a sheet structure. To add different layers, you can use a laminating machine. Finally, you can ensure the final product has the right properties through the vulcanization process.
At Renton Belt Factory, we always ensure high quality. From mixing to packing, proper quality standards are ensured at every step. Our customers are satisfied with our products. We hope you will be no exception. Contact our customer support team today if you have questions or need a quotation.